Strom statt Gas: Nachhaltige Herstellung von Karosseriebauteilen
Vor dem Hintergrund der Energiewende gerät auch die deutsche Industrie zunehmend unter Druck, Produktionsprozesse umzugestalten. Es findet ein gesellschaftlicher Wandel statt und die Nachhaltigkeit und Variabilität der Produktion gewinnt immer mehr an Bedeutung, auch um die von der Europäischen Union für das Jahr 2050 gesteckten Klimaziele zu erreichen.
Nicht zuletzt auch aufgrund der aktuellen geopolitischen Situation und der daraus resultierenden Gasknappheit sowie Preissteigerungen liegt ein Umschwung von fossilen Energieträgern hin zu regenerativen Energien verstärkt im Fokus.
Presshärten: Herstellung von Karosseriebauteilen
Presshärtbare Stähle werden seit Mitte der 80er Jahre zur Herstellung hochfester Strukturbauteile im Automobilen Leichtbau verwendet [Ber08]. Seitdem spielen sie eine wichtige Rolle bei der Einhaltung immer strenger werdender Sicherheitsvorschriften und Klimaziele.
Die Anzahl der gefertigten Bauteile pro Jahr steigt seit der Einführung des Verfahrens stetig an. Während im Jahr 1987 noch 3 Millionen Teile pro Jahr gefertigt wurden, wird die Anzahl der gefertigten Teile im Jahr 2017 auf bereits 300 Millionen geschätzt [Kar10][Pal17].
Moderne Automobilkarosserien weisen einen Anteil pressgehärteter Bauteile an der Gesamtmasse des BIW von bis zu 40% auf [Sjö18]. Dies verdeutlicht die Relevanz des Verfahrens für die Automobilindustrie und die Bedeutung, die es zur Herstellung leichter, widerstandsfähiger Karosseriekomponenten besitzt.
Allerdings machen die Emissionen, die im Fahrzeugbetrieb entstehen und maßgeblich durch den Leichtbau beeinflusst werden, nur einen Teil der Gesamtemissionen eines PKW aus. Einen weiteren wichtigen Aspekt stellt die Fahrzeugherstellung dar. Auch hier fallen Emissionen sowohl bei der Rohstoffgewinnung als auch bei der Weiterverarbeitung an.
Energie für Öfen wird durch Gasbrenner erzeugt
Im industriellen Presshärteprozess erfolgt die Erwärmung der Platinen üblicherweise in einem Durchlaufofen, wie zum Beispiel dem Rollenherdofen. Aufgrund der Wärmeübertragung im Ofen in Form von Strahlung und Konvektion werden Aufheizzeiten von bis zu 5 Minuten benötigt, um die Platinen auf eine Temperatur von 950°C zu erwärmen [Kar10][Kol11].
Damit genügend Platinen zur Einhaltung des Pressentaktes zur Verfügung stehen, müssen die Öfen entsprechend lang ausgelegt werden [Kol11][Mor17]. Dies führt dazu, dass typische Ofenlängen von mehr als 40m erreicht werden [Kol11]. Die benötigte Energie, um diese Öfen auf Temperatur zu bringen, wird standartmäßig durch Gasbrenner erzeugt. Gasbetriebene Öfen sind auf den Einsatz fossiler Energieträger angewiesen, wodurch ein Umstieg der Fertigung auf regenerative Energien erschwert wird.
Hinzu kommt, dass Rollenherdöfen einerseits lange Auf- und Abkühlzeiten besitzen, andererseits kann es bei starken Temperaturschwankungen zu einer Beschädigung der zum Stückguttransport eingesetzten Keramikrollen kommen [Zei13]. Daher werden die Öfen häufig auch während eines Produktionsstillstandes weiter beheizt, um einen reibungslosen Betrieb zu gewährleisten [Vib16]. Dies führt auch bei Stillstand einer Produktionslinie zu einem hohen Energiebedarf.
Induktion bei der Fertigung von Karosseriebauteilen – warum?
Die induktive Erwärmung bietet hier als Alternative viele Vorteile gegenüber dem konventionellen Rollenherdofen. Durch die direkt im Bauteil erzeugte Wärme können höhere Heizraten und bessere Wirkungsgrade als bei der Wärmeübertragung durch Konvektion und Strahlung realisiert werden. Dies macht die Induktion zu einem platzsparenden und energieeffizienten Verfahren zur Erwärmung von Stahlbauteilen.
Das Verfahren findet daher auch schon beim Schmelzen, Schmieden und der Wärmebehandlung von Karosseriebauteilen industrielle Anwendung [Mor17][Kol09]. Aber auch das Potential der Induktion zur Erwärmung von Blechplatinen im Presshärteprozess wurde in den letzten Jahren vermehrt untersucht [Kol09][Opi15][Trö14][Vib16][Pfe19]. Ein großer Schwerpunkt dieser Untersuchungen ist der Einfluss der induktiven Erwärmung auf die Homogenität der Erwärmung und die Bauteileigenschaften der Blechplatinen.
Im Rahmen eines AiF Forschungsprojektes (IGF-Nr. 18738) konnte ein Prozess entwickelt werden, welcher eine homogene Erwärmung von Formplatinen mittels Längsfeldinduktor im Pressentakt auf Laborebene ermöglicht. Es wurden im Projekt mit Hilfe der induktiven Erwärmung vergleichbare Bauteileigenschaften zum konventionellen Prozess erzielt.
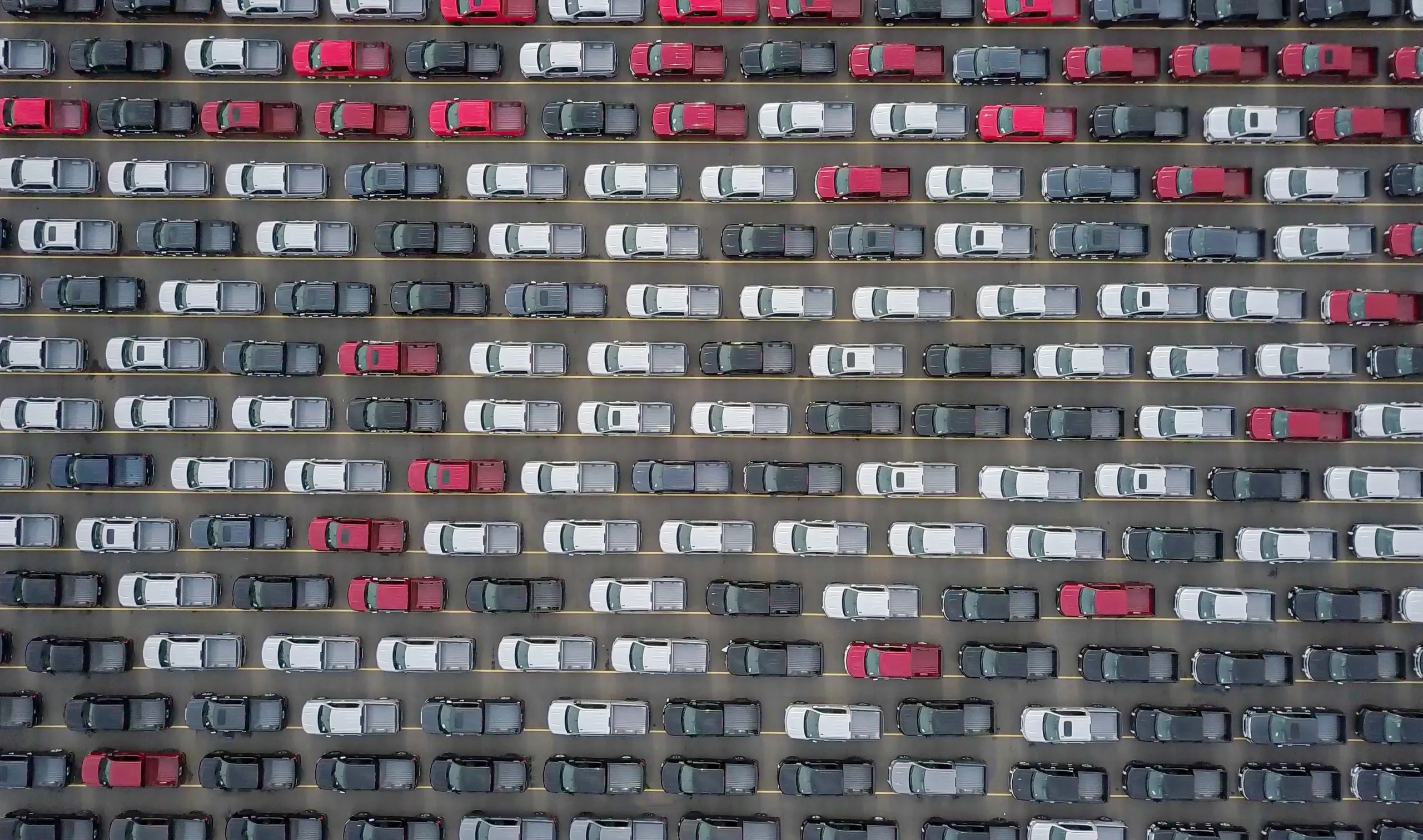
Induktion noch nicht in der Serie im Einsatz
Trotzdem bleibt dieser Technologie der Sprung in die industrielle Anwendung bisher verwehrt. Die Ursache dafür sind Unsicherheiten in Bezug auf die serielle Anwendbarkeit und den wirtschaftlichen Nutzen des Verfahrens. Dabei besitzt der Prozess großes Potential für den Aufbau einer energieeffizienten und nachhaltigen Produktionslinie.
Die auf elektrischen Energien basierende Erwärmung ermöglicht den Einsatz regenerativ gewonnenen Stroms und bietet so die Möglichkeit eines emissionsfreien Fertigungsprozesses. Durch die hohen Aufheizraten ergibt sich eine große Flexibilität in Bezug auf Fertigungszeiten, Zieltemperaturen und Stückzahlen.
Dadurch wird einerseits ein Energieabruf nur dann nötig, wenn auch wirklich Bauteile gefertigt werden, wodurch Leerlaufenergien entfallen und die Energieeffizienz der Fertigung gesteigert wird, andererseits ergeben sich so neue Möglichkeiten die Fertigungsprozesse an Losgrößen und Umwelteinflüsse anzupassen und so die Fertigung als Ganzes zu optimieren.
Re²Pli – ein Schritt in die Serie
Hier setzt das Projekt „Regenerative Energien für den effizienten Betrieb einer Presshärtelinie“ (Re²Pli) an. Auf Basis der induktiven Erwärmung soll eine nachhaltige und effiziente Fertigungslinie zur Herstellung pressgehärteter Bauteile aufgebaut und validiert werden.
Neben der Fertigung werden dabei energetische und wirtschaftliche Aspekte einer auf regenerativen Energien beruhenden Fertigungslinie betrachtet. Dadurch sollen Unsicherheiten in Bezug auf die Anwendbarkeit des Verfahrens beseitigt und Szenarien für die Implementierung in ein zukünftiges Energie- und Fertigungskonzept aufgezeigt werden.
Für das Projekt, unter der Leitung des Lehrstuhls für „Leichtbau im Automobil“ (LiA) der Universität Paderborn, hat sich das LiA mit Wissenschaftlern des Instituts für Elektrotechnik und des Software Innovation Labs der Universität Paderborn sowie mit den Unternehmen BuL Werkzeugbau, MOESCHTER Group, MORYX Industry by Phoenix Contact, Phoenix Contact Smart Business, Ulrich Rotte Anlagenbau und Fördertechnik, WestfalenWIND Planung, AEG Power Solutions, INTILION sowie Kirchhoff Automotive zusammengeschlossen.
„Re²Pli“ wird im Rahmen der Initiative „progres.nrw – Innovation“ vom Ministerium für Wirtschaft, Industrie, Klimaschutz und Energie des Landes Nordrhein-Westfalen über einen Zeitraum von drei Jahren mit rund 3,5 Millionen Euro gefördert und durch den Projektträger Jülich betreut.
Serientauglichkeit wird erforscht
Die Forschungsziele des Projektes umfassen die Serientauglichkeit des Prozesses als auch die Geschäfts- und Betriebsplanung sowie die bilanzielle Betrachtung. Zum Nachweis der Serientauglichkeit steht der Aufbau einer Produktionslinie für das Presshärten von Blechkomponenten mit induktiver Erwärmung sowie die Fertigung von Demonstrator-Bauteilen auf dem Plan.
Der Aufbau der Produktionslinie soll dabei unter dem Gesichtspunkt der Energieeffizienz erfolgen. Es sollen die Vorteile einer Induktionsanlage bezüglich des Platzbedarfs ausgenutzt werden, um ein möglichst effektives Anlagenlayout unter Berücksichtigung von Transport, Erwärmung und Umformung zu ermöglichen.
Des Weiteren steht die Ermittlung von Geschäfts- und Betriebsmodellen für eine induktiv betriebene Presshärtelinie im Fokus. Dabei sollen eng verknüpft mit dem Energiemanagementsystem Betriebsmodi für den Anlagenbetrieb ermittelt werden. Die hohe Flexibilität der induktiven Erwärmung ermöglicht eine dynamische Anpassung der Fertigungsstrategie. Damit können Größen wie Energieverfügbarkeit, Wartungen, Störungen und Rüstzeiten besser in einer Fertigungsstrategie berücksichtigt werden.
Energieeffiziente Fertigung von Karosseriebauteilen
Ziel ist es ein System zu entwickeln, was in Kommunikation mit Maschinengrößen, Energiemanagement und Auftragslage eine optimierte, energieeffiziente und wirtschaftliche Fertigung von Karosseriebauteilen ermöglicht. Zuletzt erfolgt eine bilanzielle Betrachtung der induktiv betriebenen Presshärtelinie. Dabei sollen die benötigte Energie und Rohstoffbedarfe zur Fertigung von Karosseriebauteilen ermittelt und mit bestehenden Fertigungsmethoden abgeglichen werden.
Das Ziel ist der Nachweis eines ökologisch-ökonomischen Vorteils einer mit regenerativem Strom betriebenen Fertigungslinie gegenüber der Nutzung fossiler Energieträger. Im Sinne der steigenden Nachfrage nach Lieferkettenverantwortung sollen dabei auch vorgelagerte Prozesse zur Bereitstellung der notwendigen Ressourcen berücksichtigt werden.
Literatur
[Kar10] Karbasian, H., Tekkaya, A.E.: A review on hot stamping. In: Journal of Materials Processing Technology 210 (2010) No. 15, Seite 2103-2018.
[Kol09] Kolleck R. et al.: Investigation on Induction Heating for Hot Stamping of Boron Alloyed Steels. In: CIRP Annals – Manufacturing Technology 58 (2009) No. 1, Seite 275–278.
[Kol11] Kolleck, R., Veit, R.: Current and Future Trends in the field of Hot Stamping of Car Body Parts, 3rd International Conference on Steels in Cars and Trucks, June 5-9, 2011, Salzburg, Austria.
[Mor17] Mori, K. et al.: Hot stamping of ultra-high strength steel parts. In: CIRP Annals 66 (2017) Issue 2, Seite 755-777
[Opi15] Opitz, T.; Vibrans, T.: Induktive Schnellerwärmung von Formplatinen für die Warmumformung im Karosseriebau. In: HTM Journal of Heat Treatment and Materials 70 (2015), No. 6, Seite 261-266.
[Pal17] Palm, C. et al.: Increasing performance of hot stamping systems, International Conference on the Technology of Plasticity, September 17-22, 2017, Cambridge, United Kingdom.
[Pfe19] Pfeifer, F., Marten, T., Tröster, T., Dietrich, A., Nacke, B.: Investigation on Inductive Heating of Sheet Metal for an Industrial Hot Stamping Process, Proceedings of 7th International Conference on Hot Sheet Metal Forming of High-Performance Steel, Luleå, Sweden, June 2-5, 2019, pp. 585-93
[Sjö18] Sjölin, U. et al.: The All New V60 2018 Car Body, EuroCarBody, October 16-18, 2018, Bad Nauheim, Germany
[Trö14] Tröster, Thomas: Niewel, Jörg; Salomon, Rainer: Forschung für die Praxis / Forschungsvereinigung Stahlanwendung e.V. im Stahl-Zentrum. Bd. 805: Einsatz des induktiven Erwärmens von Platinen und Ermittlung der entsprechenden Prozessfenster für das Presshärten; Düsseldorf: Verl. und Vertriebsges. mbH, 2014.
[Vib16] Vibrans, Tobias: Induktive Erwärmung von Formplatinen für die Warmumformung. Dissertation, Technische Universität Chemnitz, 2016
[Zei13] Zeichner, Achim: Entwicklung einer Ofenrollenbeschichtung für das Presshärten. Dissertation, Rheinisch-Westfälisch Technische Hochschule Aachen, 2013
Weitere Beiträge zum Thema auf unserem Blog:
„Vehicle-to-Grid“: Elektroautos als Speicher für erneuerbare Energien von Dennis Schulmeyer, LADE GmbH
Strukturwandel der Mobilität – Warum eine Verkehrswende dieses Mal gelingen sollte von
Elektromobilität: Dynamische Entwicklung allein reicht nicht von Anna Grimm und
Kommentar verfassen